Energising the Revolution
Revolutionary wellbore technology delivering unimaginable downhole power with total control.
Products & Core Technology
Our breakthrough core technologies, HydroVolve INFINITY and PolyVolve SWIVEL, are completely unique.
HydroVolve INFINITY is an infinitely versatile and controllable downhole engine unleashing unimaginable power. Use it to agitate, vibrate, resonate, motivate, generate, inflate, or perforate - an infinite number of possibilities exist.
As the world’s most advanced swivelling thrust bearing with a unique modular design, PolyVolve SWIVEL unlocks immense pull or push forces to provide an unrivalled solution to stuck object removal.
HydroVolve INFINITY and PolyVolve SWIVEL are the prime driving forces and strength behind our interchangeable product suite, allowing for unrivalled performance.
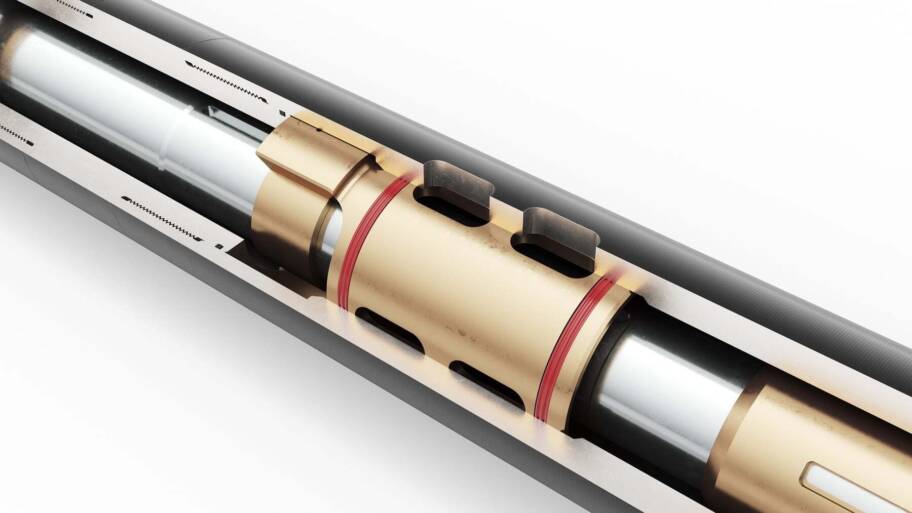
We’re delivering on our promise to bring new, unique solutions across conventional energy, geothermal and decommissioning sectors.
By listening to the challenges you’re facing, we’ve designed and engineered multiple new products to satisfy your needs and help you make operations safer, cheaper, and easier.
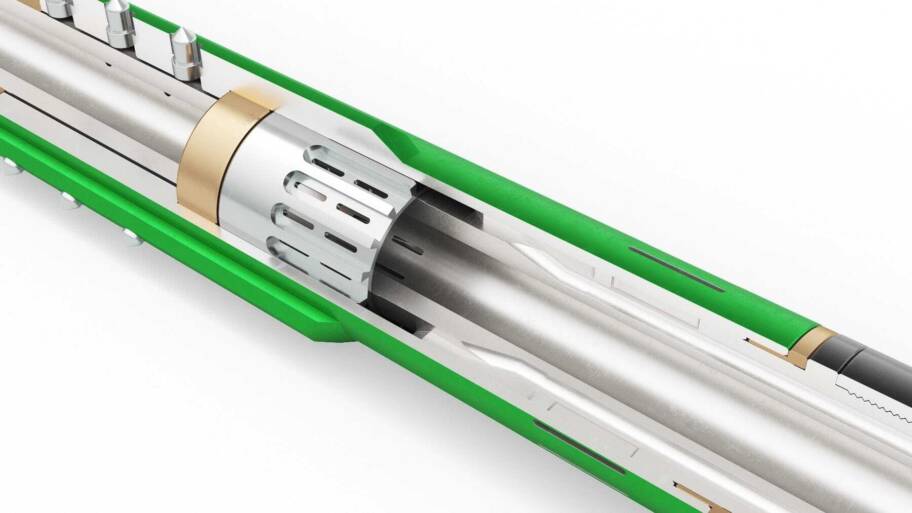
Our in-house testing facilities and team are second to none.
We’re proud to offer customers a complete end-to-end service, taking exact requirements through feasibility testing, concept design/development, and all the way to production.
We own the most advanced indoor rotary drilling test facility in Europe, enabling first trial results without the requirement to mobilise tools to remote wells and test sites.
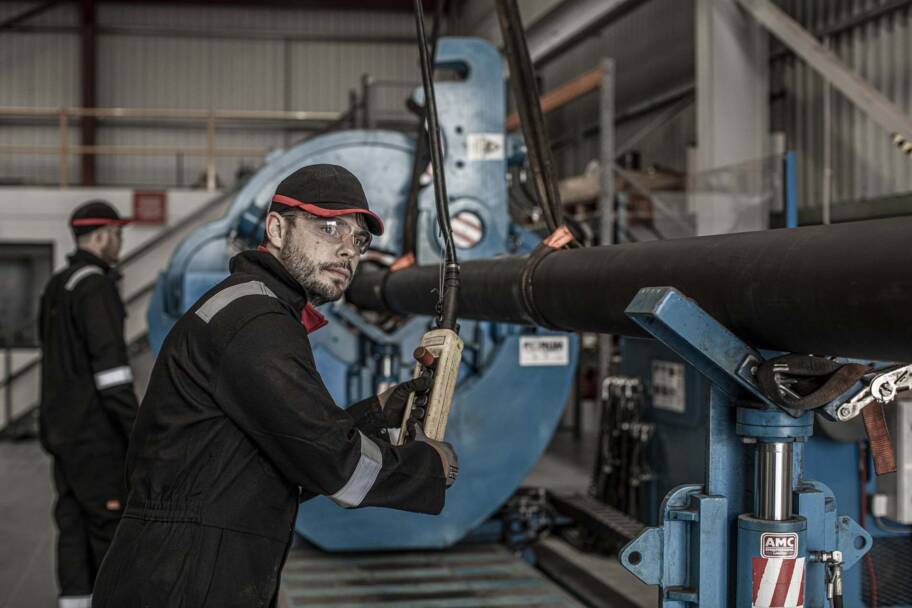